IoTは先端技術という認識もあるが、その中で人手が中心の菓子メーカーでIoT活用により予防保全を行い、成果を挙げた企業がある。石川県加賀市の竹内製菓グループである。なぜIoT活用に踏み切ったのか。同社の取り組みを追う。
製造現場におけるIoT(モノのインターネット)活用はさまざまな製造業で広がりを見せる。ただ、大きな投資で大規模に実践できるケースは一部に限られている。特に和菓子など、人手を中心とする食品製造領域では、まだまだIoTとは縁遠いのが現状である。そうした中で、IoTを活用した予防保全に取り組み成果を挙げた和菓子メーカーがある。石川県加賀市の竹内製菓グループである。
なぜ、竹内製菓グループでは、IoTを活用した予防保全を考えたのか。そこには、加賀市の支援や複数の支援企業などとの関係性があった。その背景や苦労、成果、今後の取り組みなどについて、聞いた。
原材料高騰に悩んだ、
創業70周年を迎える竹内製菓グループ
観光地の土産として、饅頭などの菓子は今でも定番となっている。そのため、温泉地の近郊にはみやげ菓子を製造する企業が工場を構えるケースが全国的にみられる。2019年で創業70周年を迎える竹内製菓グループ(石川県加賀市)もそうした菓子メーカーの1つだ。加賀温泉にほど近い場所に3つの工場を構える竹内製菓グループは、創業以来“明日の銘菓を創造する”というテーマのもと、高付加価値商品の創造に取り組んできた。現在もきんつば、くず餅、どら焼き、蒸し饅頭などの和菓子から、クッキー、チーズケーキ、フィナンシェなどの洋菓子まで幅広く観光土産菓子を製造し、空港、駅の売店などを通じて販売している。
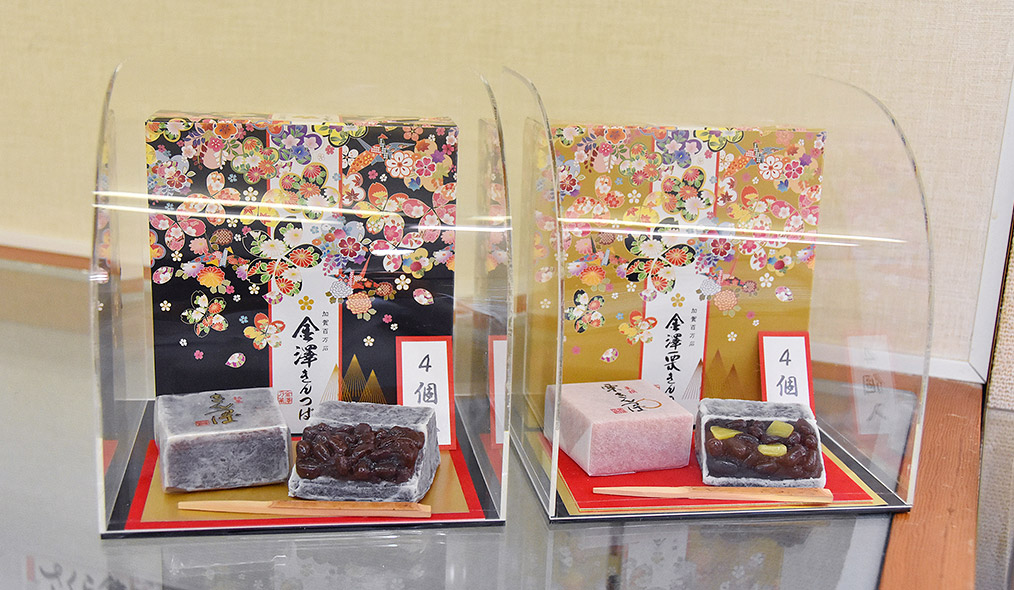
順調に業績を伸ばしてきた竹内製菓グループだが、ここ最近は原材料の高騰という問題が深刻化し、対応に苦慮していたという。そこで、原材料の高騰への対応として生産量の拡大による生産性改善に取り組み、原価上昇を生産効率で補う取り組みを進めることにしたという。
「あずきや砂糖などの原材料や、ラッピングに使うフィルムなどの価格が高騰し、これらに対応していく必要がありました。厳しい市場競争があるため、商品の価格を上げることは難しい状況でした。そこで、社内体制の効率化に取り組み、その1つとして生産量増による生産効率向上に取り組むことを考えました」と竹内製菓グループ 取締役 統括本部長の清水良一氏は説明する。
実際に生産数量を増やすために、新たな製造機械を導入した。しかし、導入直後は求めるパフォーマンスを発揮したものの、徐々にパフォーマンスが落ち、求める生産量を維持できなくなるという現象が発生したという。「生産性改善のために新たに導入したのに、想定パフォーマンスが全く出ない状況が生まれていました」と清水氏は語る。
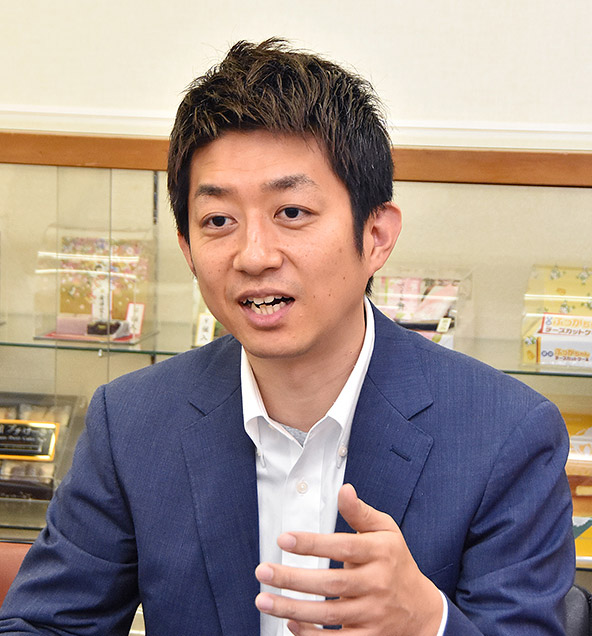
取締役 統括本部長
清水 良一 氏
当初計画数量に遅れが発生する「きんつば」焼成機
同社が生産性改善のためにまず新たな製造装置を入れたのは、主力商品の1つである「きんつば」の製造工程だ。きんつばは、羊羹の周囲に小麦粉を水で溶いた生地をつけて鉄板で焼いた和菓子である。金沢(石川県)の土産としても有名で、安定した需要を誇る人気商品である。きんつばの製造には専用の焼成機を用いる。この焼成機の新たな機械を導入したわけである。従来の機械は1分間に33個を焼き上げたが、これを同40個に引き上げるため、2016年に導入した。
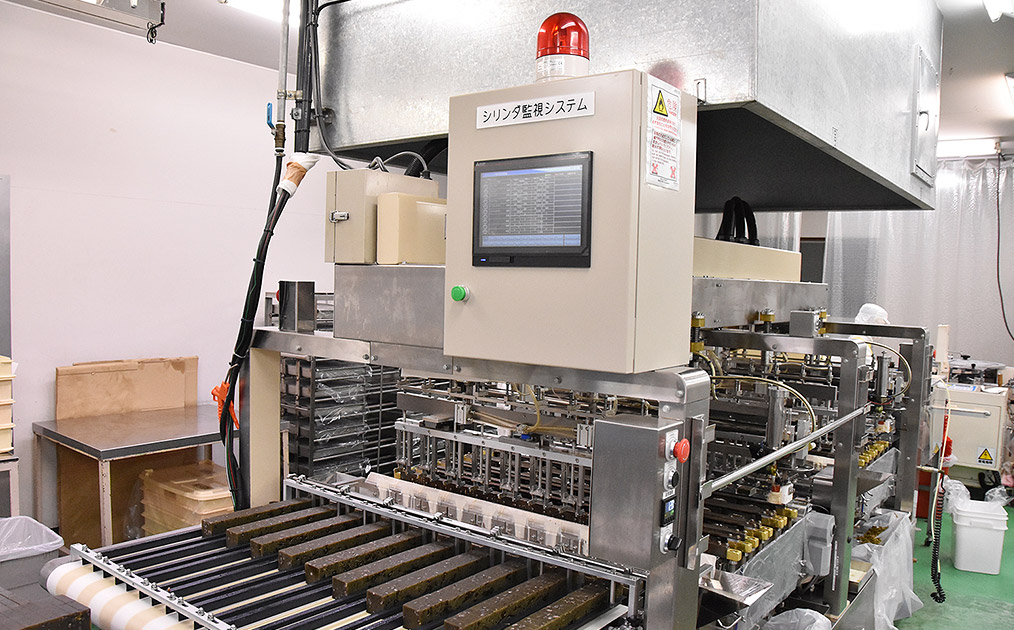
焼成機での製造工程は以下のような工程で進む。
- 1.羊羹をつかむ
- 2.羊羹に生地をつける
- 3.鉄板に食用油を塗る
- 4.羊羹を鉄板に置く
- 5.以上の工程を角度や面を変えて複数回繰り返す
- 6.冷却工程に羊羹を移動させる
- 7.出来上がった製品を包装工程に移す
これらの複雑な作業を、機械に内蔵された約40本のエアシリンダーが連動して動作することで、同時並行的に行う。
ただ、導入当初は仕様通り1分間に40個を焼くことができたが、連続稼働していくと、徐々に生産能力が低下した。気付けば生産スピードは1分間に37~38個に落ち込み、計画とのずれが生じてしまっていた。結果として生産量を確保するため、現場の担当者は、遅くまで残業しなければならない日もあったという。
能力が予定通りに発揮できていないことは現場の一部の担当者からも報告があった。気づいた段階で、その都度メンテナンスを行い、能力の回復に努めリカバーをしてきた。しかし、生産スピードの低下は一日に20分~30分程度であることから1回1回の機械の動作を見ているだけでは微量すぎて気付けない。結果として、メンテナンスを行うタイミングが遅れ、作業時間が伸びるという状況が生まれていた。
そこで、なぜ、テストの段階では能力通りに生産できたのに、実際には能力が発揮できないのかを調べた。スピードが落ちる原因については、エアシリンダーに問題があることが予想されたという。
同社 メンテナンスシニアバイザーの荒井昭雄氏は「焼成機での製造工程で、きんつばの生地を焼く直前に鉄板に食用油を塗る作業があります。これは、エアシリンダーにより油塗装置が作動し鉄板に油を塗るというものです。ただ、工程上、この作業が完全に終わらないと次の焼く作業に移らない仕組みとなっていました。ですから、油塗りが遅くなると、全体の遅れとなり、生産能力が低下するという構造です。エアシリンダーは、ほぼ全ての工程に使われていますが、生産性に影響を与えるのはこの油塗りの工程だろうという当たりはついていました」と要因について述べる。
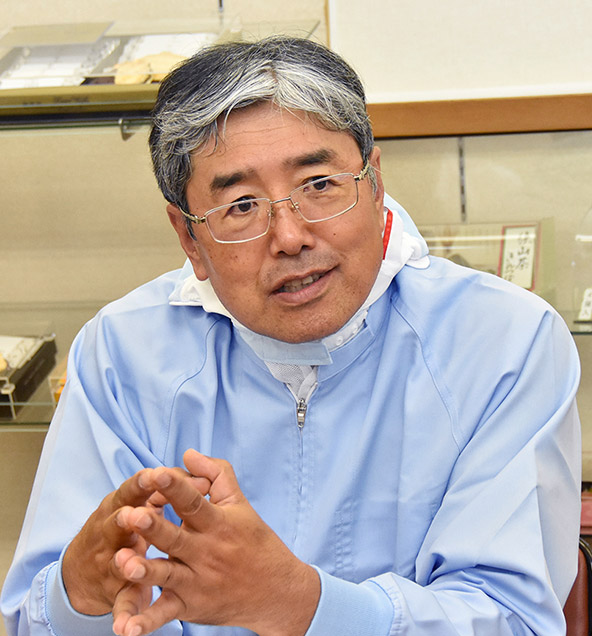
メンテナンスシニアバイザー
荒井 昭雄 氏
油塗りのエアシリンダーの動作時間は端から端まで動作して、通常は約2.7秒かかる。仮にこれが3.1秒になると、一日あたり600個の生産が減少する計算となる。当時のメンテナンスでは、遅延が分かった段階でエアシリンダーの汚れ、摩耗による細かな傷などを取り去り、機械油をエアシリンダーに差すなどして能力を改善していた。しかし、担当者によってはタクトタイムでの0.4秒の遅れは気付かないこともある。「この課題についてどうしようか悩んでいたところで出会ったのが、IoTを活用した製造監視システムです」と清水氏は語る。
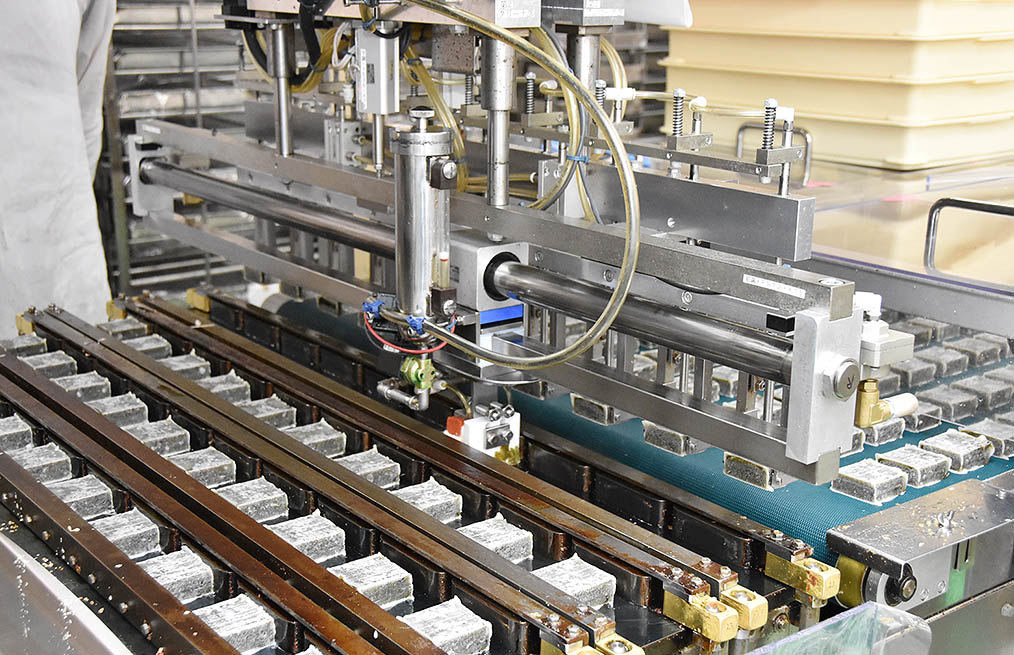
IoTによる焼成機の予防保全を実現
今回、IoT活用のきっかけとなったのは、e-F@ctory Allianceパートナーである立花エレテックからの提案があったからだという。「当初はIoTがどのようなものか、費用がどのくらいかかるか、それを導入して果たして解決するか、など全く分かりませんでした」と清水氏は当時を振り返る。しかし「立花エレテックからの提案で、三菱電機の『e-F@ctory』ソリューションの1つにシリンダを監視するシステムがあることを聞き、ちょうどわれわれの課題にぴったりだと感じました。そこで一気に関心が高まりました」(清水氏)。
焼成機のパフォーマンス低下の問題は「遅延が現場では見えない」ということだった。そこで、IoT導入による課題解決の方向性としては「エアシリンダーの一挙動の開始から終了までのタクトタイムを毎回取得する」ということに置いた。そして、エアシリンダー1挙動のタクトタイムの上限時間を設定し、その設定時間をオーバーしたら、遅延とみなし、アラートを出して担当者に気付きを与えるという仕組みである。
一方で、焼成機のシーケンサー(PLC)から情報を取得するためのI/F(インタフェース)において、きんつば焼成機の機械制御そのものには影響を与えないことなどの条件を設定した。荒井氏は「遅れている気付きを的確に情報にして与えることに特にポイントをおいた」と強調している。
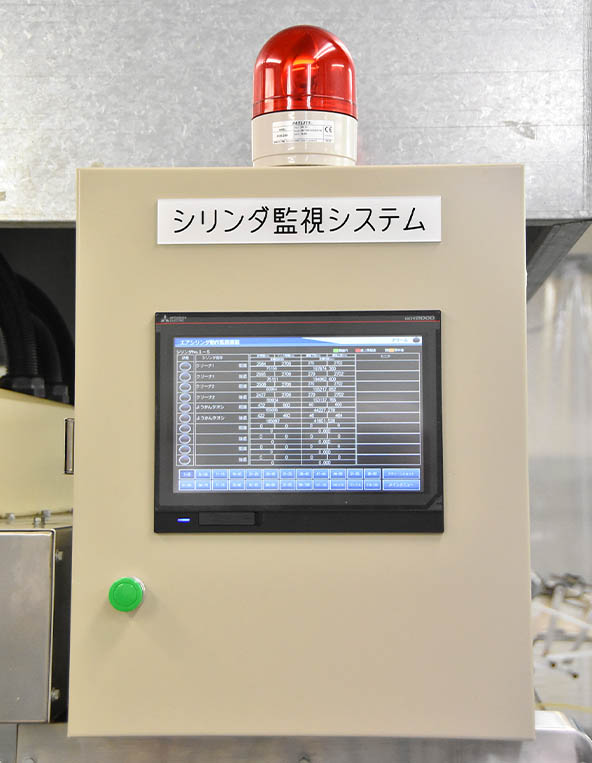
規定時間をオーバーしたら赤いランプが点灯する
三菱電機の「e-F@ctory」で導入が容易に
今回、竹内製菓グループが導入したベースとなったのは三菱電機の「シリンダ監視システム」である。三菱電機は、展開するFAとITを連携させるモノづくりコンセプト「e-F@ctory」を展開しているが、その中で簡単に導入を進められるような「e-F@ctory支援モジュール
」というサンプルプログラム集を用意している。そこで、シリンダを監視する機能があり、それを用いることで製造工程監視システムを構築することができたという。
「当社だけではプログラム作成することができないという課題もありましたが、三菱電機から汎用的なプログラムを用意してもらえた事。さらに、立花エレテックからの支援も受けられ、ローコストで導入が進められたというのが採用の決め手の1つになりました」と清水氏は支援体制について語る。
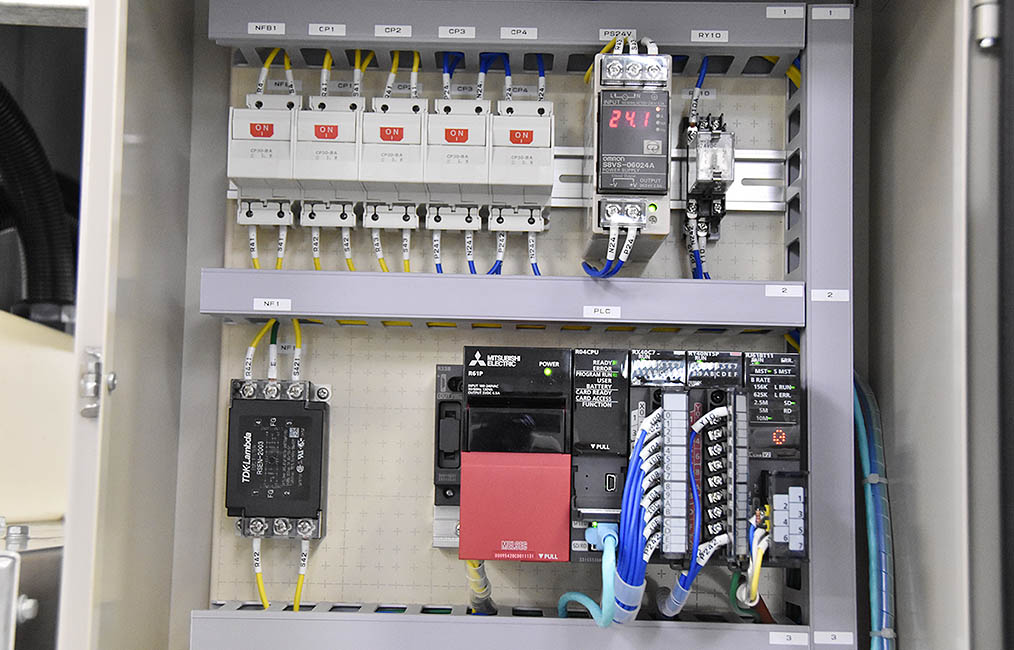
また、竹内製菓グループのある石川県加賀市はIoT機器を使って生産性の向上を目指す企業に対して、補助金を交付する「製造業におけるIoT導入実証事業」制度(当時100万円を限度に全額補助)などを展開しており、これも大きな後押しとなったという。「IoTで実際に価値が生まれるのかは分からなかったので、スモールスタートから始めようと考えていました。その点で、補助金制度の存在は大きかった」と清水氏は振り返る。
この他、対象となった焼成機が、三菱電機のシーケンサー(PLC)を使っていたことという幸運もあったようだ。ただ、今回の監視システムと焼成機をつないだ時に、機械の補修、メンテナンスをどうするかなど、保守契約上の細かい点で問題が残った。これらは竹内製菓グループと機械メーカー、立花エレテックの3社で話し合いを行い、契約上の問題もクリアすることができたという。
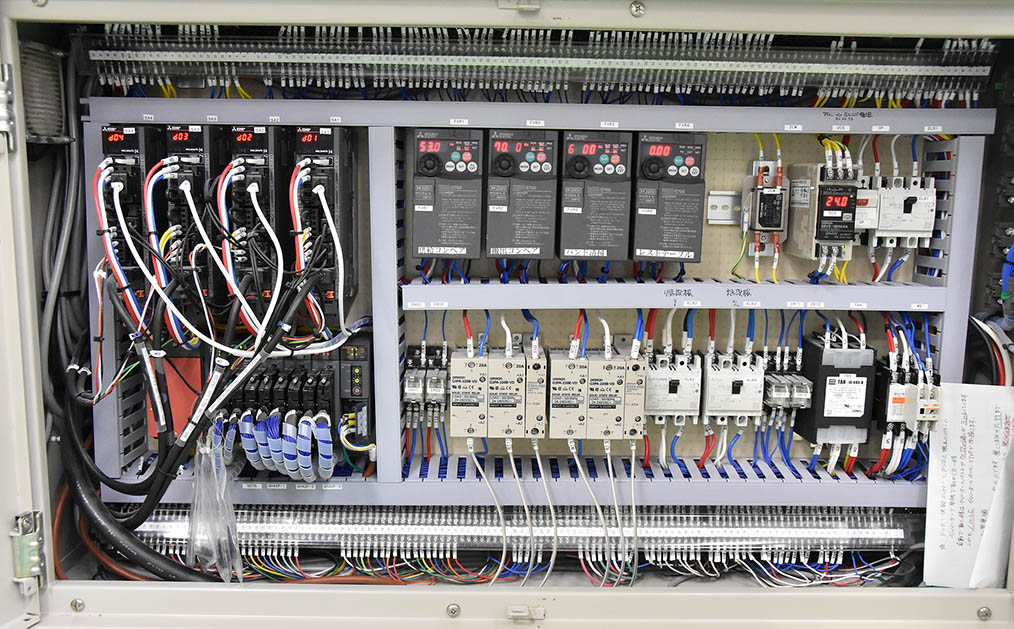
最終的には、2018年12月にきんつば焼成機とのインタフェースの調査や打ち合わせ、スペックの確認を実施。2019年1月上旬からタクトタイム監視を行い、同下旬からその評価を開始したという。
これらの評価結果を見ると、現在は大きな生産性改善が見られているという。最適なメンテナンスタイミングを把握することで、パフォーマンスを落とすことなく生産が進められている他、生産量などもキメ細かく情報を取得することで、さらなる効率向上につながり、導入時に見込んだ1分間に40個を上回る同42個を達成しているという。予定値よりも5%向上するパフォーマンスを生み、生産量が上がったため、社員の残業が減るなど働き方の面でも好影響を与えているという。
この他、それまでの「勘」に頼る部分もあったメンテナンスも「ポイントを絞って対応できることから、指導もしやすくなりました。結果も出ており、従業員の負担が削減されました」(荒井氏)。さらに、比較的高価であるエアシリンダーなどはメンテナンスを効果的に行うことで部品の長寿命化などのメリットも生まれているという。清水氏は、今回の投資は「補助金が無くても損益的にプラスになっています」(清水氏)と経営面でも手応えをつかんでいる。
AIを活用した予兆保全や、ラインの稼働時間見える化を
「e-F@ctory支援モジュール」には、この他の機能も豊富に用意されていることから、竹内製菓グループでは今後、監視システムをエアシリンダーだけではなくモーターの振動測定など、他にも広げることを検討しているという。さらに、メンテナンスは、これまで現場のスタッフで手分けして実施してきたが、不具合が重なった場合など対処できないこともあるため、AIなどを活用した予兆保全
などの採用なども検討するという。
さらに、将来的にはラインの稼働時間の見える化などにも取り組む方針だ。竹内製菓グループには現在3つの工場があり、合計で13ラインが稼働している。ラインの中には毎日稼働するものと週1~2回稼働するものがあるなど、稼働時間に大きな差がある。同社の場合、製造する商品に合わせてラインを組み替えることも多い。ただ、現状では「フル稼働した日」「切り替えを行うなど計画停止した時間」「不具合により停止した時間」など、それぞれの稼働状況をリアルタイムに把握できているわけではない。
今後、そうした稼働時間を見える化することで、停止している時間の長いラインについては廃止し、稼働時間の長いものについてはラインを増やすことなど選択と集中を図るための、基本データの収集、分析などを行いたい意向である。清水氏は「今回の取り組みにより、見える化することで状況を大きく改善できるということが分かりました。一気に大きく導入することは難しいですが、社内でまだまだ余力を生み出す余地があると考えています。IoTを活用することでこうした隠れたリソースを作り出せるようにしていきます」と今後の抱負を述べている。
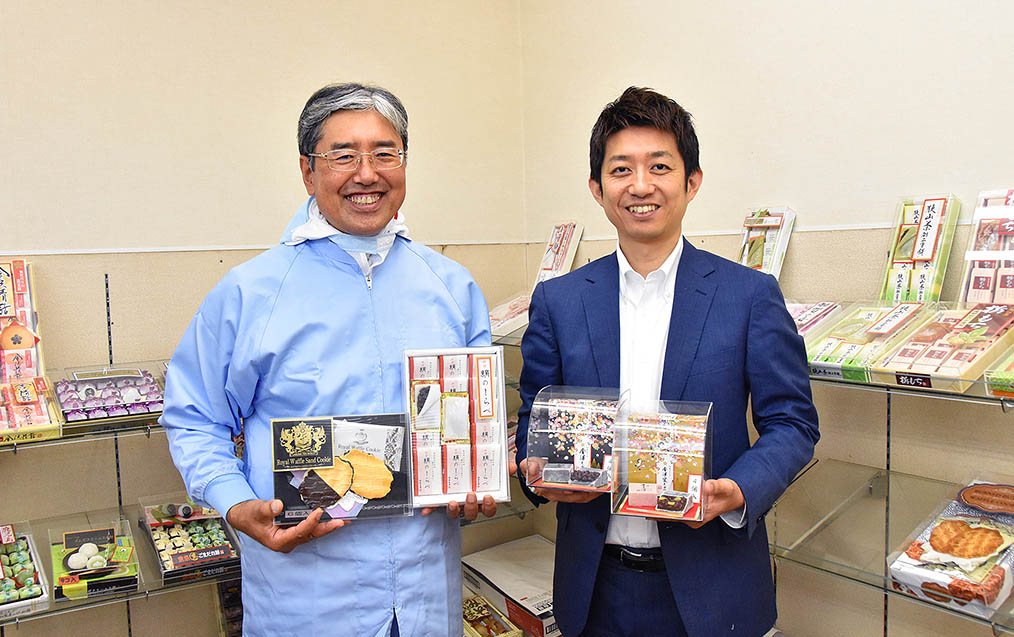
転載元:MONOist
MONOist 2019年8月19日掲載記事より転載
https://monoist.atmarkit.co.jp/
mn/articles/1908/19/
news004.html
本記事はMONOistより許諾を得て掲載しています