目的別ソリューション
設計・立上効率化ソリューション
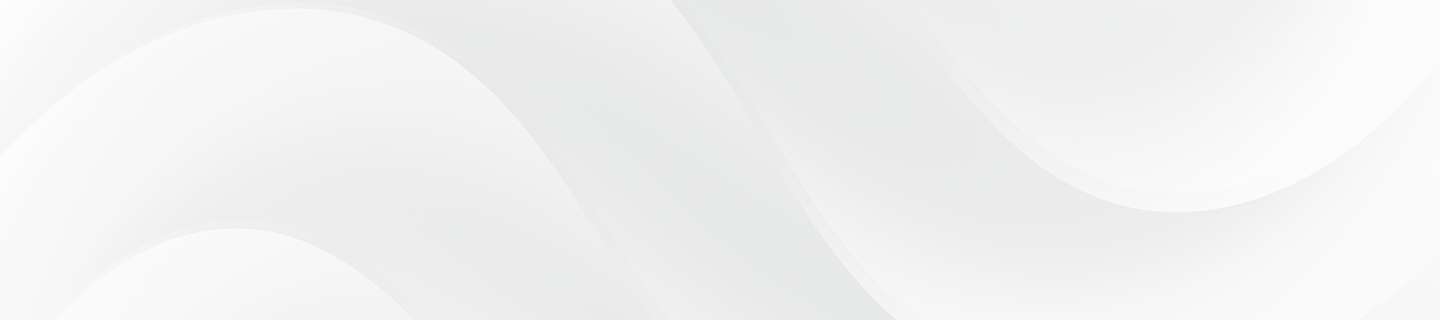
課題
手戻り削減のため、デバッグの品質を向上したい
制御設計者向け
デバッグ時に気づけなかった不具合により、立ち上げ時に装置のメカ干渉が発生したり、サイクルタイムが想定より長いといった事象が発生している。立ち上げ時に制御プログラムを修正して対処しているが、手戻りが大きいため何とかしたい。
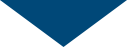
各エンジニアリングツールのシミュレータを用いて制御プログラムのシミュレーションを行うだけでなく、3Dシミュレータ MELSOFT Geminiと接続することで、装置の動作やサイクルタイムを実機レスで事前検証。
Point1 制御プログラムのシミュレーション
シーケンサ、表示器、モーション、ロボットの各エンジニアリングツールには、制御プログラムのシミュレータを内蔵。実機が無くても、設計どおりに各制御プログラムを作成できているかを検証することが可能です。

Point2 装置動作のシミュレーション
3Dシミュレータ MELSOFT Geminiを各エンジニアリングツールのシミュレータと接続することで、制御プログラムの動作を3Dモデル上で視覚的に確認でき、ロボットの干渉やサイクルタイムなどのプログラム上だけでは気づきにくい不具合を発見できます。
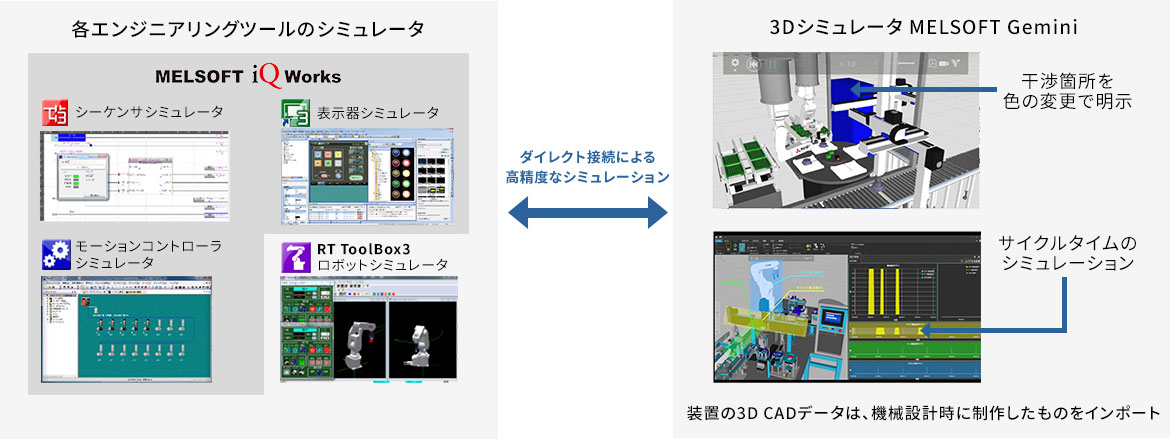
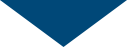
装置動作の異常やメカ干渉、サイクルタイムなどを実機レスで事前検証することで、現地での手戻りを大幅に削減
導入事例

装置シミュレーションで設計・立上期間を約15%短縮導入!
生産現場での立ち上げ時に多大な調整時間を要していたA社。装置シミュレーションを導入し設計のフロントローディングを実現することで、設計・立上期間を約15%短縮することに成功した。その秘訣とは?
設計どおりの生産能力を出せるか立ち上げ前に確認したい
工程設計者向け
工程設計時にラインバランスや作業者の負荷率を考慮しているものの、制御設計時の仕様変更などの影響で、実際にラインを立ち上げてみると設計どおりの生産能力を出せておらず、ラインバランスやレイアウトの見直しといった手戻りが発生している。
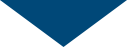
工程設計・機械設計時に制作した3Dモデル(ライン、設備)と、制御設計時に制作した装置の制御プログラムを用いて、デジタル空間上に実機と同等の高精度な生産ラインモデルを構築し、生産能力を最終確認。
Point1 高精度な3D生産ラインの構築
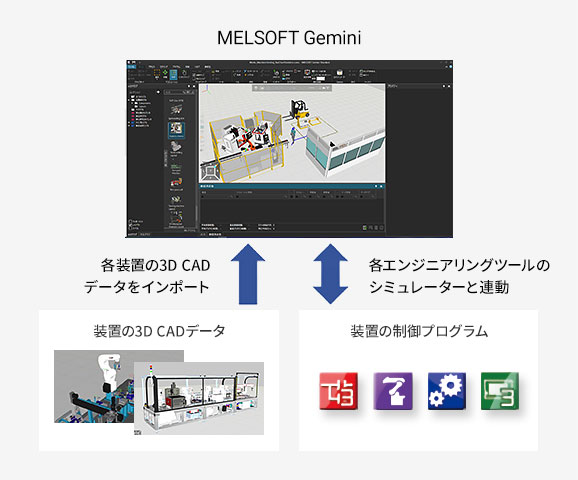
工程設計時に制作したラフな生産ラインモデルを元に、機械/制御設計時に制作した各装置の3D CADデータを取り込み、更に制御プログラムと連動させることで、パソコン上に高精度な生産ラインモデルを構築できます。
Point2 ラインシミュレーションで最終確認
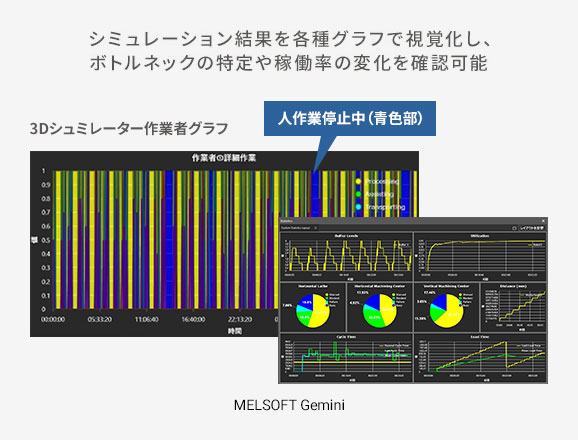
高精度な生産ラインモデルを用いて、立ち上げ前にラインシミュレーションを再度実施することで、ラインバランスや作業者の負荷率などを高精度に確認。工程設計時と立ち上げ時のギャップを最小化できます。
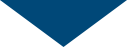
生産ラインモデルの高精度化により、工程設計時と立ち上げ時のギャップを最小化し、手戻りを削減
現地調整時のトラブルシュートを効率化したい
立ち上げ作業者向け
制御設計者向け
現地調整時に設備トラブルが発生した際は、現場を訪問しトラブル時の挙動を確認した上でトラブルシュートを実施しているが、トラブルの再発を現場で長時間待つことや、現場が遠方の際に出張コストが大きい場合があるため、効率化したい。
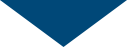
システムレコーダを用いてトラブル時のデータをまるごと記録し、パソコン上で挙動を再現しトラブルの根本原因を追跡できるようにすることで、遠隔地にいながら簡単にトラブルシュート。
Point1 トラブル時のデータをまるごと記録
もし立ち上げ時にチョコ停などのトラブルが発生したとしても、シーケンサのレコーダユニット/カメラレコーダユニットを活用することで、トラブル前後のデバイスデータやカメラ映像、表示器の操作履歴などをまるごと記録可能。トラブル原因を特定するために、再びトラブルが起きるまで現場に常駐する必要はありません。
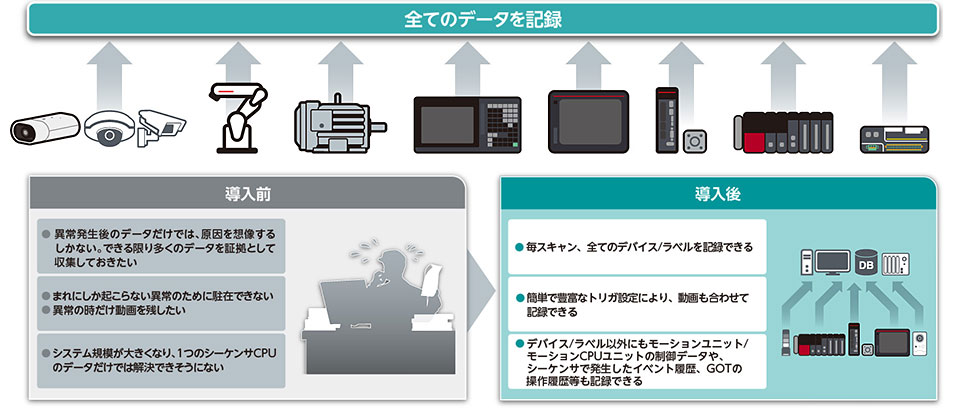
Point2 遠隔地から簡単にトラブルシュート
記録したデータと設計時に用いた3Dシミュレータ MELSOFT Geminiを用いて、トラブル時の設備動作をパソコン上で再現。遠方の立ち上げ現場を訪問することなく、自席でトラブル原因を特定することが可能です。もし現地での対処が必要な場合でも、あらかじめ準備をした上で訪問できるため、ムダがありません。
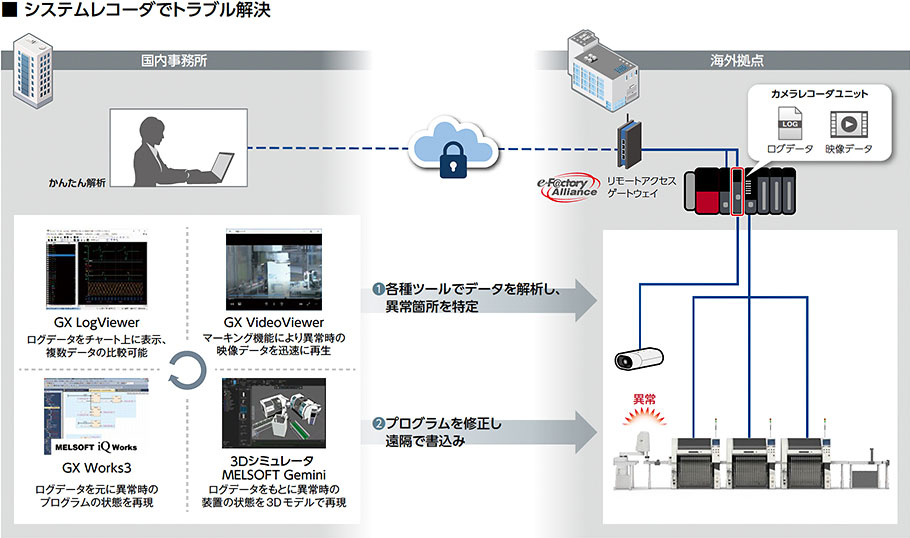
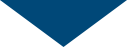
トラブル原因を簡単に特定できるだけでなく、立ち上げ現場を訪問するための時間や出張費用を削減
導入事例
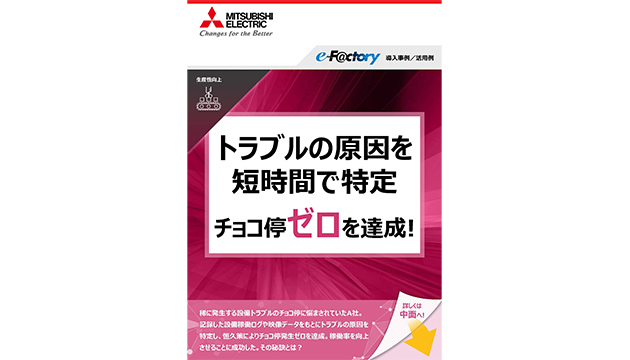
トラブルの原因を短時間で特定 チョコ停ゼロを達成!
稀に発生する設備トラブルのチョコ停に悩まされていたA社。記録した設備稼働ログや映像データをもとにトラブルの原因を特定し、恒久策によりチョコ停発生ゼロを達成。稼働率を向上させることに成功した。その秘訣とは?