開発NOTE
ゼロベースからスタートし、
努力を重ねここまでカタチに。
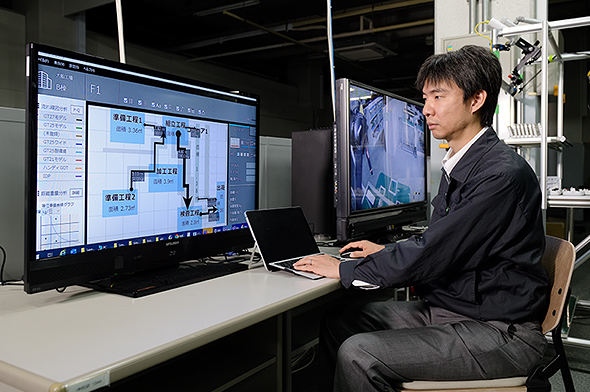
情報技術総合研究所 櫻井 智史
生産性改善とひと言で言っても、様々な視点で取り組みが行われています。「骨紋®」がひとりひとりの作業を改善するための技術であるのに対し、「生産ライン改善支援技術」は現場の環境を改善するための技術です。
この開発を始めた当初、我々は生産性改善についての知識が乏しく素人同然でした。生産性改善とは何か、フロアレイアウトの設計はどんなプロセスでなされるのか、どんな技術があれば役に立つのか等々、社内の生産性改善に携わる部署の方々はもちろん、大学の教授など、たくさんの人にお話しをお聞きすることから始めました。
また、開発の途中では弊社の工場のフロアレイアウト変更にこのツールを使い評価をいただくなど、多くの専門家・経験者のアドバイスを受けながら改善に努めてきました。さらにこの技術の開発には、AIやGUIの専門家など異なる分野の技術者の協力も欠かせませんでした。
文字通りゼロベースから開発を始め、ここまでやっとたどりつけたというのが正直な感想です。
これまでにないフロア設計専用ツールを作りたかった。
いままで生産ラインのフロア設計は、多くの場合ほぼ手作業で行われていました。レイアウトとモノの流れを別々に設計するために、モノを運ぶ経路を確保し損ねるなどのミスも出やすく、何度もやり直すなど、手間と時間のかかる作業でした。特に専用ツールはなく、一般的なオフィスソフトを使い、勘や経験が頼りでした。高額な3Dシミュレーターを使えば、レイアウト設計からモノの流れのシミュレーションまでを行うこともできますが、使いこなすまでに時間かかる等、導入には高いハードルがあります。
このような現状を打破するのが今回の技術です。レイアウトとモノの流れをひとつの画面で、整合性を取りながら簡単に設計でき、レイアウト変更に伴う生産量の変化も高精度でシミュレーションすることが可能です。
平均値ではなくリアルな値を、そのためにAIが必要でした。
生産量をシミュレーションするには、それぞれの作業時間を算出する必要があります。 同じ作業であっても作業時間にバラツキが生じるため、たとえば複数回計測してその平均値でシミュレーションを行うなどの方法が採られていました。
今回の技術では単なる平均値ではなく、現場の実態に近い作業時間をAIで算出し、シミュレーションを行います。どうしても起きる作業時間のバラツキ、さらには作業ミス、作業を始めた朝と一日働いて疲労がある夕方との作業時間の変化。これらの要素を考慮したシミュレーションモデルを「Maisart®」を活用して作成しました。
平均値ではく、より正確な作業時間を割り出すためにはどうしたらいいか、その答えがAIを活用することでした。このような用途でAIを活用した例はいままでなかったかもしれません。
まずは課題を洗い出し、製品化というゴールを目指します。
製品化をひとつのゴールとするならば、この技術はまだスタートラインに立ったばかりです。生産ラインは千差万別です。今後はまず色々なラインでの検証を重ね、機能の拡充やGUIの改善など、課題を洗い出すことが必要だと思っています。
技術は使ってもらって何らかの役に立ってこそ価値が生まれます。まだまだ道程は長いかもしれませんが、この技術を製品化し、誰かの役に立つものにしたい、そう強く思っています。
今回、生産現場の方々にヒヤリングし、現場の厳しさを肌で感じました。秒単位でいかに生産の効率化を図っていくか、日夜努力を続けておれらます。この技術もそうですが、生産性改善は手作業で行われている部分が多く、まだまだ我々技術者にできることがあるのでは、そう感じています。
関連商標:「Maisart」、「骨紋」は三菱電機株式会社の登録商標です。